PIONEERS.
PRODUCT INNOVATORS.
DIVERS.Photo by John Bantin
OUR MISSION…
To help divers dive better – explore further, stay longer and enjoy the ride along the way. We do this by designing and manufacturing innovative (often revolutionary) products that are easy-to-use but enhance diver performance – even in the harshest conditions. Everything we make is conceived, tested and assembled in our factory and research centre in the heart of Cornwall, UK. We aim:
- To be the be the best in everything we do from the boardroom to the shop-floor.
- To help educate, support and inform the worldwide diving community wherever we can. Our doors are always open to divers who wish to visit and we’re happy to discuss any aspect of diving – from the operation of rebreather units, to specific dive plans, to advice on DIY servicing and repairs, the supply of custom tools or any other questions you may have. This is not a hollow promise. Give us a call to arrange a visit.
- To adopt a no-compromise-on-quality approach to every product we make.
- To enjoy diving with the kit we make.
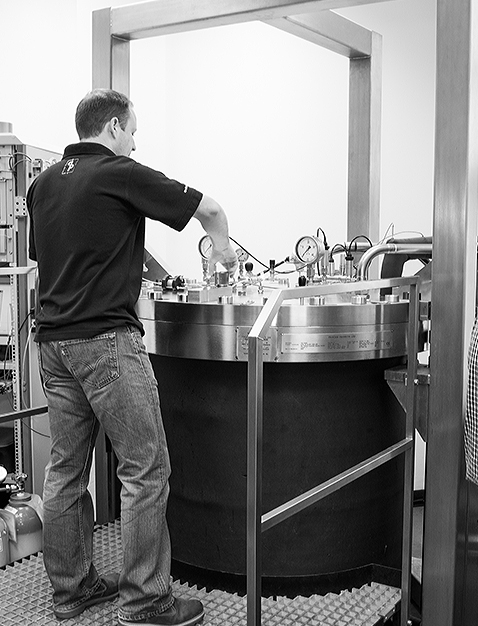
Right now we’re pushing the boundaries of technical and sport diving through advanced product development – producing kit that allows divers to unlock their potential and expand their dive horizons safely, efficiently and in comfort. Our 6th generation Inspiration range of closed circuit rebreathers is a testament to our constant R&D drive-to-improve. Through extensive research and punishing test regimes we aim to make equipment for divers that is built properly, works well and tackles the snag-points and problems we all come across underwater. Where that will lead us next, we’re not always sure.
But that’s just part of the adventure.

WHY WE BUILD THINGS THE WAY WE DO
With in-house design, tool-making and manufacturing we can ensure start to finish quality and consistency in our manufacturing processes, build quality and product specifications which are routinely inspected and verified by third party agents Lloyd’s Register Quality Assurance Ltd to achieve the essential ISO 9001 manufacturing standard. We manufacture 95% of all products – right down to the brass and plastic components – in-house.
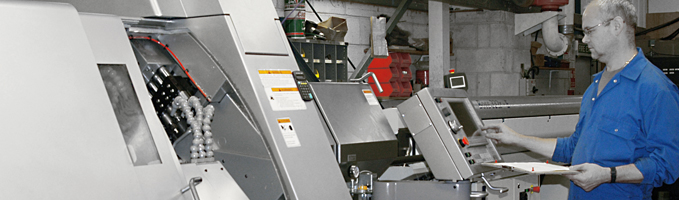
We realise this approach goes completely against the grain of other manufacturers’ thinking. Most of them have been off-shoring production for decades. We make no apology for keeping it local… it’s what we do. Experience has taught us that if ever there is a problem, it’s usually created by an external supplier. Keeping it in-house we retain that family-business ethos – pride in what we do and quality control over the whole process. Start to finish.

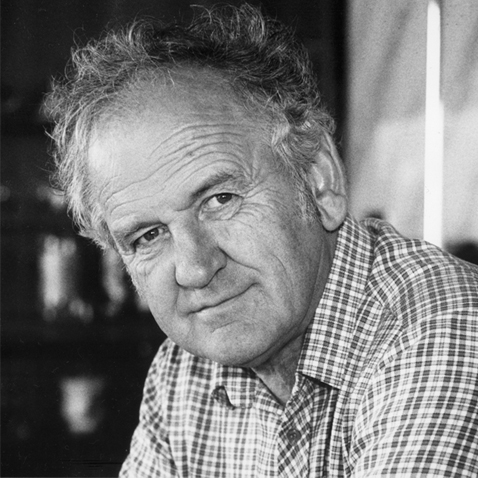
OUR STORY
For more than 45 years, AP has led the way in diving – innovating, designing and manufacturing equipment of the highest quality. Since its foundation in 1969, the company has grown at a phenomenal rate, from a small family-business to an internationally respected dive manufacturer with a global network of great dive instructors, distributors and support centres. Our customers range from individual sport and professional divers, to search & rescue services, the military, police, fire service, bomb disposal, ship’s divers and coastguards through to the commercial giants of the salvage, shipping and oil industries – in over 50 countries worldwide.
How have we achieved this? We never make and sell anything we’re not 100% happy to use as divers ourselves. Today, every area of the factory from the design office to the boardroom, from the sales office to the shop floor is staffed with divers of all training backgrounds and experience.
This, combined with our manufacturing philosophy, ensures we are committed to design excellence, to production quality and to solving the problems divers face underwater every day. In fact, this endless quest for better dive kit was where our story began…
Back in 1969, the founders of the company, keen sport divers David & Angela Parker, saw the need for a more effective ‘out-of-air’ emergency-breathing system. There was nothing available anywhere so they set about inventing one. The result, the now famous AP Valve automatic mouthpiece, allowed divers to breathe easily from their air-inflated buoyancy jacket, providing panic-relieving air on demand in those critical first few seconds of an out-of-air emergency. Shortly after this invention, AP developed their own range of buoyancy jackets – the famous BUDDY range of BCDs (now renamed the AP range) – and together with the inspired addition of a BCD mini-cylinder, the AP Valve became a lifesaver, invaluable to generations of divers.
The concept, so simple and reliable, has withstood the test of time and is present today in evolved forms in the Auto Air octo-inflator and the APV200 power inflator – available as options on the full range of AP buoyancy jackets and wings.
We have grown from tiny beginnings, quite literally, a garden shed at the back of our dive-shop / hardware store in Coventry – Parker Hardware – to a leading international dive company renowned for the quality of our equipment. How? By focusing on 3 things: quality, trust and service. We innovate and manufacture superior quality products, fairly priced, that cater for the extremes of what is an exciting but ultimately, dangerous sport; we always try to offer straightforward, honest advice to divers; and we always go the extra mile – taking a genuine pride in our products & services.
We build 95% of all components ourselves in-house. This means that from initial idea, to design, tool-making, machining, molding, assembly, final inspection and testing right through to the finished product – we have complete control over the things we create.
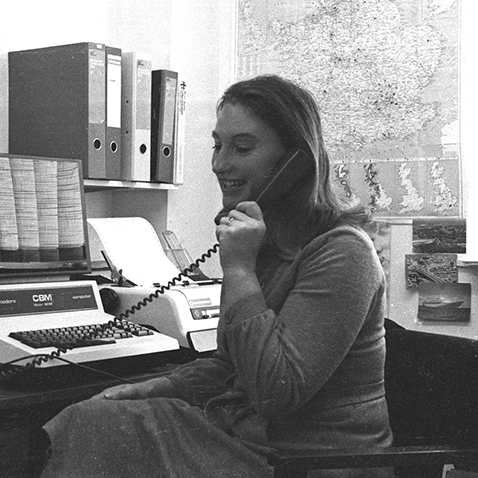

OUR PEOPLE
There are currently 55 people working here in our manufacturing and innovation centre in Cornwall, UK. Nearly all of them dive. (The few that don’t are shown endless dive and underwater exploration films from the 1970s in our re-education room… until they do.)
We have product designers, engineers and test-divers working away at solving the problems divers face – constantly looking for ways to make your dive better, more comfortable, more exciting.
We have attracted and retained some of the best people in the dive & manufacturing industries, who are not only proud of the products they make but are proud to offer an after-sales service that is second to none – clearly made so much easier by having continuous production and ready availability of spares.